The 25-Second Trick For Alcast Company
The 25-Second Trick For Alcast Company
Blog Article
The 9-Minute Rule for Alcast Company
Table of ContentsThe Single Strategy To Use For Alcast CompanyFascination About Alcast CompanyAbout Alcast CompanyThe Definitive Guide to Alcast CompanyAbout Alcast CompanySome Of Alcast Company
The subtle difference depends on the chemical material. Chemical Contrast of Cast Aluminum Alloys Silicon advertises castability by reducing the alloy's melting temperature and boosting fluidity throughout spreading. It plays an essential role in permitting complex mold and mildews to be filled up properly. In addition, silicon adds to the alloy's toughness and use resistance, making it important in applications where sturdiness is essential, such as automobile parts and engine parts.It additionally enhances the machinability of the alloy, making it simpler to process right into finished products. In this method, iron adds to the general workability of aluminum alloys.
Manganese adds to the stamina of aluminum alloys and improves workability (Foundry). It is typically made use of in functioned aluminum items like sheets, extrusions, and accounts. The presence of manganese aids in the alloy's formability and resistance to splitting during fabrication procedures. Magnesium is a light-weight component that supplies strength and effect resistance to light weight aluminum alloys.
The Single Strategy To Use For Alcast Company
It permits the production of lightweight components with excellent mechanical residential properties. Zinc improves the castability of light weight aluminum alloys and assists manage the solidification procedure throughout casting. It boosts the alloy's strength and solidity. It is usually discovered in applications where intricate shapes and great details are needed, such as ornamental spreadings and specific auto parts.
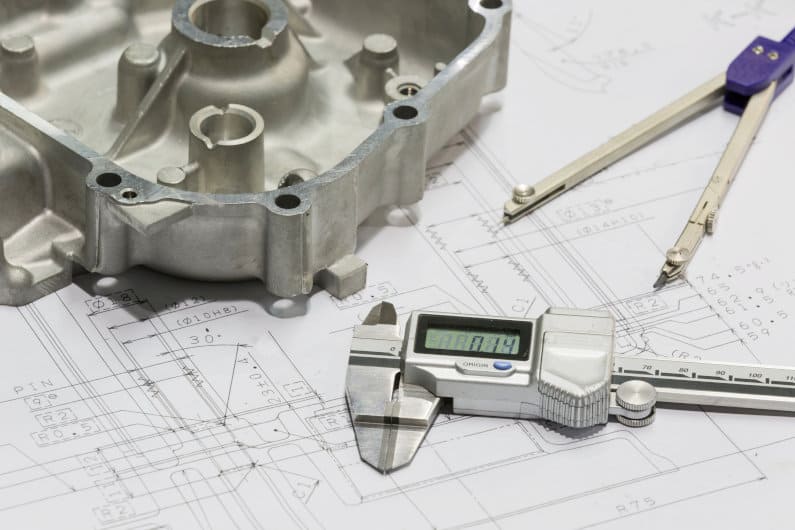
The main thermal conductivity, tensile stamina, yield stamina, and prolongation differ. Among the above alloys, A356 has the highest thermal conductivity, and A380 and ADC12 have the least expensive.
The Alcast Company Statements

In accuracy casting, 6063 is well-suited for applications where elaborate geometries and top notch surface area finishes are paramount. Examples include telecommunication units, where the alloy's exceptional formability permits for sleek and aesthetically pleasing layouts while maintaining architectural honesty. In a similar way, in the Lights Solutions industry, precision-cast 6063 parts develop stylish and reliable lighting components that require elaborate forms and good thermal performance.
It leads to a finer surface coating and far better corrosion resistance in A360. Moreover, the A360 displays premium elongation, making it excellent for complicated and thin-walled components. In precision casting applications, A360 is well-suited for markets such as Customer Electronics, Telecommunication, and Power Devices. Its enhanced fluidness allows for elaborate, high-precision elements like smart device casings and communication gadget real estates.
See This Report about Alcast Company
Its one-of-a-kind residential properties make A360 a beneficial selection for accuracy casting in these industries, boosting product durability and high quality. Aluminum alloy 380, or A380, is a commonly used casting alloy with a number of unique attributes. It provides excellent castability, making it an ideal choice for precision casting. A380 shows good fluidness when molten, making sure elaborate and detailed molds are accurately replicated.
In accuracy spreading, light weight aluminum 413 beams in the Customer Electronic Devices and Power Tools sectors. It's commonly utilized to craft detailed elements like smart device housings, cam bodies, and power device coverings. Its precision is amazing, with limited resistances as much as 0.01 mm, making certain remarkable item setting up. This alloy's remarkable corrosion resistance makes it an exceptional selection for outdoor applications, guaranteeing resilient, resilient products Discover More Here in the mentioned sectors.
The Ultimate Guide To Alcast Company
As soon as you have decided that the aluminum die casting process is suitable for your task, a crucial next action is selecting one of the most appropriate alloy. The light weight aluminum alloy you select will considerably affect both the casting process and the properties of the last item. Due to this, you have to make your choice meticulously and take an educated method.
Establishing the most suitable aluminum alloy for your application will imply evaluating a large selection of characteristics. The very first classification addresses alloy qualities that affect the manufacturing process.
The Single Strategy To Use For Alcast Company
The alloy you select for die casting straight impacts a number of aspects of the spreading procedure, like how easy the alloy is to function with and if it is susceptible to casting flaws. Hot breaking, additionally referred to as solidification cracking, is a normal die casting issue for light weight aluminum alloys that can cause inner or surface-level splits or fractures.
Specific light weight aluminum alloys are more prone to hot cracking than others, and your selection must consider this. Another typical defect located in the die spreading of aluminum is die soldering, which is when the actors adheres to the die walls and makes ejection difficult. It can damage both the cast and the die, so you must try to find alloys with high anti-soldering homes.
Corrosion resistance, which is already a significant attribute of aluminum, can differ considerably from alloy to alloy and is a vital particular to take into consideration depending upon the environmental problems your product will certainly be exposed to (aluminum casting manufacturer). Put on resistance is one more residential or commercial property commonly sought in aluminum products and can distinguish some alloys
Report this page